Best bitcoin exchange to western union
13 comments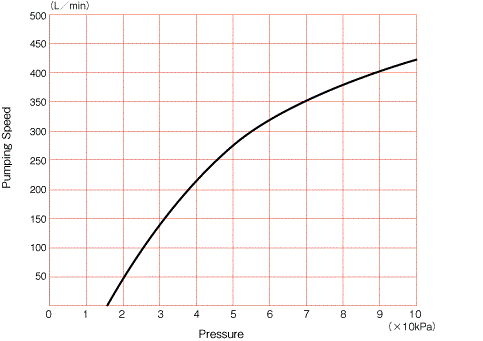
Bitcoin wallet password recovery tool
To receive news and publication updates for International Journal of Rotating Machinery, enter your email address in the box below. A corrigendum for this article has been published. To view the corrigendum, please click here.
Correspondence should be addressed to Si Huang ; nc. This is an open access article distributed under the Creative Commons Attribution License , which permits unrestricted use, distribution, and reproduction in any medium, provided the original work is properly cited.
Liquid ring pump is widely applied in many industry fields due to the advantages of isothermal compression process, simple structure, and liquid-sealing.
With the major geometric parameters and operating conditions of a liquid ring pump, the performance parameters such as the actual capacity for suction and discharge, shaft power, and global efficiency can be conveniently predicted by the proposed theoretical model, without the limitation of empiric range, performance data, or the detailed 3D geometry of pumps.
The proposed theoretical model was verified by experimental performances of liquid ring pumps and could provide a feasible tool for the application of liquid ring pump.
Liquid ring pump is a kind of rotary displacement machines, including liquid ring vacuum pump and liquid ring compressor. Owing to the advantages of isothermal compression process, simple structure, and liquid-sealing, liquid ring pump is widely applied in petroleum, chemical, power, metallurgy, pharmaceutical, and light industry and other fields, particularly suitable for the pumping of flammable, explosive, toxic, and harmful gases like hydrogen, oxygen, nitrogen, chlorine, ethylene, acetylene, propane, natural gas, and carbon dioxide.
However, there are still some problems such as a higher power consumption, lower suction vacuum degree, and unstable operation in application of liquid ring pump. The theoretical result considerably deviates from the actual performance due to the lack of the fundamental study on the performance and restricts the improvement of performance and reliability of liquid ring pump.
Therefore, it is of significant scientific and application values to carry out the fundamental study on the operating theory and performance of the liquid ring pump. The operating principle of the liquid ring pump is illustrated in Figure 1.
With the revolution of the impeller, the operating liquid is ejected outwards due to centrifugal forces and forms a liquid ring. Owing to the eccentricity of the impeller to the casing, a crescent-shaped chamber forms between the impeller hub and the liquid ring. The impeller blades divide the crescent-shaped chamber into several cells of different volumes.
As the impeller runs, the cells in the range of the suction port become larger and suck the gas through the suction port. In the part opposite to the suction port, the gas is compressed in the reducing cells and emitted through the discharge port.
Each revolution of the impeller corresponds to one operating cycle. Consequently, liquid ring pumps are the rotating machines with reciprocating pump characteristics and the ring liquid takes on the function of a reciprocating piston. Since the first liquid ring pump was invented, many scholars have carried out a variety of work on the design and industrial application of liquid ring pumps [ 1 — 6 ]. Compared with the work on the other types of pumps and compressors, however, there were few reports of the fundamental studies on liquid ring pumps.
Schulz [ 8 ] and Segebrecht [ 9 ], respectively, deduced similar equations for the theoretical suction capacity. So far, the theoretical model and the equations of theoretical suction capacity have been mainly used as reference for design of liquid ring pump.
As shown in Table 1 , the theoretical suction capacity, determined by the impeller rotational speed and the geometric parameters of liquid ring pump, remains constant regardless of the compression ratio of discharge pressure to suction pressure. This result obviously deviates from the actual situation, especially when the compression ratio is relatively high. To solve this problem, Prager [ 10 ] correlated an empirical formula for the ratio of the actual suction capacity to the maximum actual suction capacity, based on experimental performance data of liquid ring pump, but the validity of the statistical formula was restricted by the number of samples and the unknown maximum actual suction capacity.
On the other hand, it was found from the actual applications that the minimum suction pressure of the liquid ring pump was close to the saturated vapor pressure of the operating liquid. Thus, Powle [ 11 ] developed an equation for the ratio of the actual discharge capacity to the maximum actual discharge capacity as a function of vapor pressure of the operating liquid and index of expansion process in the pump, but the maximum actual discharge capacity should be given in advance.
Concerning the power of liquid ring pump, due to the absorption and the removal of the heat by the operating liquid, the gas compression process in the liquid ring pump is generally regarded as isothermal one, so the formula for the isothermal compression power of the ideal gas is commonly used to calculate the effective power of the liquid ring pump [ 12 , 13 ]. Bodik [ 14 ] deduced an approximate relation between the shaft power and rotational speed of liquid ring pump Table 1.
Recently, some investigators [ 15 — 18 ] used CFD numerical approach to simulate 3D flows and predicted performance of liquid ring pumps. Although numerical approach plays an important role for understanding internal flow field of liquid ring pump, it is still hard for practical application, due to the restriction of detailed 3D geometry of liquid ring pump, consumption of computation time, and the accuracy of gas-liquid two-phase flow model.
In this paper, therefore, a convenient and universal theoretical model is proposed for the performance prediction of liquid ring pump based on the actual operating cycle, to obtain the rules of operating cycle performance and of power consumption in liquid ring pumps, without limitation of statistical range or the detailed 3D geometry.
During the suction process Curves shown in Figure 2 a , the suction pressure keeps constant and reaches the maximum suction capacity. In the compression process Curves , the gas volume reduces and the pressure increases to reach the discharge pressure. In the discharge process Curves , the discharge pressure keeps constant and all the gas is discharged from the pump.
Like the actual operating principle of reciprocating compressor, however, some residual gas capacity is is still available in the liquid ring pump after gas discharge and returns to the suction zone; the residual gas changes to in capacity after a process of expansion Curves in Figure 2 b and goes to the next operating cycle.
Thus, the actual operating cycle is composed of four processes: The actual suction capacity in a liquid ring pump is if ,. The residual gas and its expansion process were not taken into account in the theoretical model for ideal operating cycle of liquid ring pump, resulting in deviation between theoretical and practical results.
Therefore, the theoretical model in the present work is to supplement an expansion process on the basis of the ideal operating cycle model. For the integrity of the model, the formulas in each zone are given in detail below. The definition of geometric parameters in the liquid ring pump is shown in Figure 3. The distance from any point on the liquid ring surface in the suction zone to the center of the impeller is expressed as where Theoretical suction capacity is defined as the gas volume flow through the OA section assuming that the liquid ring pump inhales fully: The distance from any point on the liquid ring surface in the compression zone to the center of the impeller is The compression ratio of the pressure at the circumferential angle to the suction pressure needs to solve an algebraic equation: The distance from any point on the liquid ring surface in the discharge zone to the center of the impeller is expressed as 4 Expansion Zone.
The distance from any point on the liquid ring surface in the expansion zone to the center of the impeller is also calculated by 6.
Therefore, the full shape of liquid ring surface in the liquid ring pump can be obtained according to 1 , 4 , and 6. The capacity of gas returning to the suction zone of liquid ring pump is calculated by where is the distance from the liquid ring surface at the circumferential angle to the center of the impeller.
The gas capacity changes to after a polytropic expansion process and then enters the next operating cycle: Therefore, the actual suction capacity of liquid ring pump is expressed as Then the actual discharge capacity can be calculated according to the isothermal compression process: The effective power of the liquid ring pump is generally calculated according to the isothermal compression power.
However, accurate prediction of shaft power is essential for estimating global efficiency and studying how to reduce power consumption in a liquid ring pump.
The shaft power is mainly composed of two parts: The total power consumption of the gas is the adiabatic compression work: The empirical formula of the liquid friction loss in liquid ring pump for the turbulent flow was given by Prager [ 19 ]: By referring to the formula of disk friction power in centrifugal pump [ 20 ], the equation 12 of liquid friction loss can be corrected as Therefore, the shaft power of liquid ring pump is written as The global efficiency is finally estimated by the following expression [ 13 ]: To validate the feasibility of the proposed theoretical models on performance of liquid ring pumps, the performance tests of the liquid ring pumps were performed.
Three types of single-stage double-acting liquid ring vacuum pumps 2BE, 2BE, and 2BE were selected for performance tests. The design and operating parameters of the liquid ring vacuum pumps are listed in Table 2. The tests were performed under different rotational speed of the pumps by frequency control.
A multiparameter data acquisition and processing system were used in the performance tests and the detailed measurement method was introduced in [ 21 ]. The experimental facility and the layout of measurement device are shown in Figure 4.
From the performance curves, it can be seen that the results of 9 under the adiabatic expansion process are close to the test results. This indicates that the expansion process of the residue gas is near the adiabatic one due to a shorter expansion time and path. Figure 6 shows the comparisons between the tested shaft power values and theoretical ones by 15 in liquid ring pump under different rotational speeds.
From Figure 6 , it can be seen that the trends of the shaft power curves calculated by 15 agree well with the ones of the test results. This means the effect of axial width of the impeller should be taken into account for liquid friction loss in liquid ring pump. More sophisticated models for shaft power of liquid ring pump are necessary to consider for higher predictive accuracy in further work.
Some conclusions are summarized as follows: The expansion process is likely near the adiabatic one due to a shorter expansion time and path. Home Journals About Us. International Journal of Rotating Machinery. Indexed in Web of Science. Subscribe to Table of Contents Alerts.
Table of Contents Alerts. Abstract Liquid ring pump is widely applied in many industry fields due to the advantages of isothermal compression process, simple structure, and liquid-sealing. Introduction Liquid ring pump is a kind of rotary displacement machines, including liquid ring vacuum pump and liquid ring compressor.
Diagram - of gas operating cycle in a liquid ring pump. Comparisons of curves between the test and theoretical models. Comparisons of curves between the test and theoretical model. Schulz, The Pumps , Berlin, Germany, View at Scopus H. Conventional and Hermetic Design, View at Google Scholar K.
Impeller eccentricity, , m. Coefficient in friction power considering effect of impeller width,. Adiabatic index; for air,. Coefficient considering the effect of blade thickness, 0.
Ratio of hub radius to impeller radius,.