Bitcoin mining chart gpu
27 comments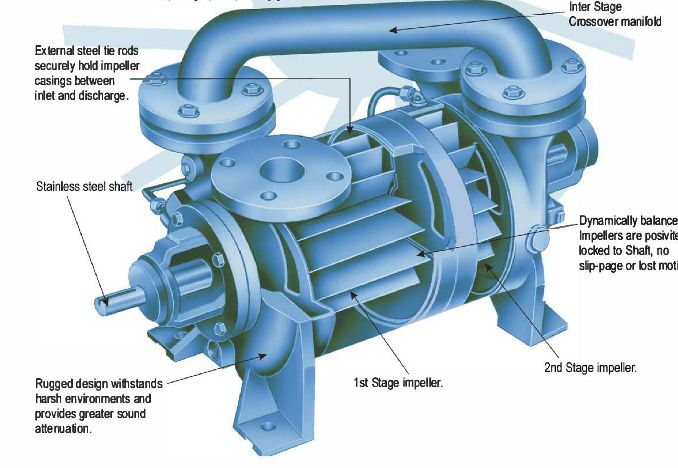
Dapps ethereum price
A liquid-ring pump is a rotating positive-displacement pump. They are typically used as a vacuum pump , but can also be used as a gas compressor. The function of a liquid-ring pump is similar to a rotary vane pump , with the difference being that the vanes are an integral part of the rotor and churn a rotating ring of liquid to form the compression-chamber seal. They are an inherently low-friction design, with the rotor being the only moving part.
Sliding friction is limited to the shaft seals. Liquid-ring pumps are typically powered by an induction motor. The liquid-ring pump compresses gas by rotating a vaned impeller located eccentrically within a cylindrical casing. Liquid usually water is fed into the pump and, by centrifugal acceleration, forms a moving cylindrical ring against the inside of the casing.
This liquid ring creates a series of seals in the space between the impeller vanes, which form compression chambers. The eccentricity between the impeller's axis of rotation and the casing geometric axis results in a cyclic variation of the volume enclosed by the vanes and the ring. Gas, often air, is drawn into the pump through an inlet port in the end of the casing.
The gas is trapped in the compression chambers formed by the impeller vanes and the liquid ring. The reduction in volume caused by the impeller rotation compresses the gas, which reports to the discharge port in the end of the casing. Compressed gas on discharge of pump contains certain amount of working liquid which is usually removed in vapor—liquid separator. The earliest liquid-ring pumps date from , when a patent was granted in Germany to Siemens-Schuckert. US Patent 1,,, for liquid-ring vacuum pumps and compressors, was granted to Lewis H.
Around the same time, in Austria, Patent was granted to Siemens-Schuckertwerke for a similar liquid-ring vacuum pump.
Liquid-ring systems can be single- or multistage. Typically a multistage pump will have up to two compression stages on a common shaft. In vacuum service, the attainable pressure reduction is limited by the vapour pressure of the ring-liquid. As the generated vacuum approaches the vapour pressure of the ring-liquid, the increasing volume of vapor released from the ring-liquid diminishes the remaining vacuum capacity. The efficiency of the system declines as a result.
Single-stage vacuum pumps typically produce vacuum to 35 Torr mm Hg or 47 millibars 4. Some ring-liquid is also entrained with the discharge stream.
This liquid is separated from the gas stream by other equipment external to the pump. In some systems, the discharged ring-liquid is cooled by a heat exchanger or cooling tower , then returned to the pump casing. In some recirculating systems, contaminants from the gas become trapped in the ring-liquid, depending on system configuration.
These contaminants become concentrated as the liquid continues to recirculate, eventually causes damage and reduced life to the pump.
In this case, filtration systems are required to ensure that contamination is kept to acceptable levels. In non-recirculating systems, the discharged hot liquid usually water is treated as a waste stream.
In this case fresh cool water is used to make up the loss. Environmental considerations are making such "once-through" systems increasingly rare. These simple, but highly reliable pumps have a variety of industrial applications. They are used to maintain condenser vacuum on large steam-turbine generator sets by removing incondensable gasses, where vacuum levels are typically 30—50 mbar.
They are used on paper machines to dewater the pulp slurry and to extract water from press felts. Another application is the vacuum forming of molded paper-pulp products egg cartons and other packaging.
Other applications include soil remediation, where contaminated ground water is drawn from wells by vacuum. In petroleum refining, vacuum distillation also makes use of liquid-ring vacuum pumps to provide the process vacuum.
Liquid-ring compressors are often used in vapor recovery systems. Liquid-ring vacuum pumps can use any liquid compatible with the process, provided it has the appropriate vapor pressure properties, as the sealant liquid. Although the most common sealant is water, almost any liquid can be used.
The second most common is oil. Since oil has a very low vapor pressure, oil-sealed liquid-ring vacuum pumps are typically air-cooled. For dry chlorine gas applications concentrated sulfuric acid is used.
The ability to use any liquid allows the liquid-ring vacuum pump to be ideally suited for solvent vapor recovery. If a process, such as distillation or a vacuum dryer, is generating toluene vapors, for example, then it is possible to use toluene as the sealant, provided the cooling water is cold enough to keep the vapor pressure of the sealant liquid low enough to pull the desired vacuum.
Ionic liquids in liquid-ring vacuum pumps can lower the vacuum pressure from about 70 mbar to below 1 mbar. From Wikipedia, the free encyclopedia. Ionic liquids — designable materials for high-performing fluids. Retrieved from " https: Webarchive template wayback links.
Views Read Edit View history. In other projects Wikimedia Commons. This page was last edited on 30 March , at By using this site, you agree to the Terms of Use and Privacy Policy. Wikimedia Commons has media related to Liquid-ring pumps.